一、前言
在汽車上應(yīng)用的鋁合金主要包括壓鑄件、鍛造件、擠壓件和板材。在這 4 類產(chǎn)品中,用于沖壓的變形鋁合金板是鋁合金板材中技術(shù)要求最高的。變形鋁合金板材替代傳統(tǒng)鋼材時(shí)可以有效減輕汽車質(zhì)量。如鋁合金發(fā)動(dòng)機(jī)蓋板和鋼制零件相比,可降低質(zhì)量40%以上。同時(shí)由于鋁合金導(dǎo)熱性好,可有效降低發(fā)動(dòng)機(jī)的溫度。除此之外,利用鋁合金的特殊性能,可以有效減輕碰撞時(shí)對(duì)行人碰撞的傷害,有利于滿足對(duì)行人碰撞保護(hù)法規(guī)的實(shí)施。目前用于汽車車身的鋁合金板材主要包括5000 系和 6000 系,常見的材料牌號(hào)如 5052、5754、5182、6016、6014、6181。此外,少量 2000 系板材也在汽車上有一定應(yīng)用。
鋁合金用于汽車覆蓋件時(shí)的性能要求極高,因此在生產(chǎn)過程中必須對(duì)關(guān)鍵環(huán)節(jié)進(jìn)行控制。在原材料生產(chǎn)階段需要對(duì)材料進(jìn)行成分設(shè)計(jì)、熔煉和鑄造,均勻化熱處理后通過冷、熱軋制工藝將材料制備成不同厚度規(guī)格的板材,最終通過熱處理控制組織及第二相來實(shí)現(xiàn)滿足生產(chǎn)需求的產(chǎn)品。在整個(gè)生產(chǎn)過程中,合理的成分設(shè)計(jì)和熱處理流程的制定是保證高質(zhì)量板材的必要前提。然而,與傳統(tǒng)軟鋼相比,鋁合金板材在成形過程中仍然存在劣勢(shì),如回彈大、容易開裂,這些劣勢(shì)需要在模具和工藝上進(jìn)行優(yōu)化和彌補(bǔ)。因此,為解決開裂和回彈問題,通常借助于有限元手段,從成形技術(shù)或工藝方面進(jìn)行鋁合金板材應(yīng)用研究。
二、車身用鋁合金的微合金化及熱處理
在鋁合金中添加微量元素,可以提高其綜合力學(xué)性能。如稀土元素加入鋁合金中,可以改善和細(xì)化鋁合金的組織,提高鋁合金的力學(xué)性能,同時(shí)還可以防止偏析,去除合金中的雜質(zhì)。鋁合金板通過一定熱處理工藝后,可以改善其組織和力學(xué)性能,具有更好的成形性。
1
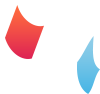
2000系合金的微合金化
2000 系合金是 Al(鋁)-Cu(銅)系合金,是 1種可熱處理強(qiáng)化的鋁合金。它具有優(yōu)良的鍛造性能、焊接性能以及烘烤強(qiáng)化效應(yīng)。合金中的主要強(qiáng)化相為 CuAl2,含有一定量 Mg(鎂)時(shí)還有CuMgAl2強(qiáng)化相,具有較高的屈服和抗拉強(qiáng)度,但抗腐蝕性能較差。2000 系合金中除主加元素外,Cd(鎘)、Ag(銀)2 種元素的單獨(dú)加入或者復(fù)合添加均可以顯著增強(qiáng)該系合金的時(shí)效硬化效應(yīng)。微量 In(銦)的添加使 Al-Cu-Li(鋰)合金的屈服強(qiáng)度增加 25%,到達(dá)時(shí)效峰值的時(shí)間縮短 25%,時(shí)效24 h 后的屈服強(qiáng)度提高70%。此外,微量元素的添加還能夠有效改善鋁合金的斷裂韌性、抗應(yīng)力腐蝕及抗疲勞性能。2091合金中微量Zn(鋅)的存在顯著增強(qiáng)了材料的斷裂韌性,如添加 Zn 質(zhì)量分?jǐn)?shù)為0.7%可使 2091 合金的臨界應(yīng)力強(qiáng)度因子值提高3.0 MPa·m1/2;微量 Ce(鈰)的添加能有效改善 Al?Cu4.5合金的抗熱疲勞性能。
文獻(xiàn)研究了加入Sc(鈧)和 Zr(鋯)元素對(duì)的2618 合金性能的影響,發(fā)現(xiàn) Sc 和 Zr 的加入使 2618合金產(chǎn)生一個(gè)初晶相Al3(Sc,Zr)。該相在凝固時(shí)可以作為非均勻形核的核心從而細(xì)化晶粒。由α(Al)固溶體析出的第二相顆粒Al3(Sc,Zr)與基體完全共格,具有明顯的析出強(qiáng)化效果。同時(shí)也使 S’相析出更加均勻。有 Al3(Sc,Zr)相的 2618 合金室溫與高溫的屈服強(qiáng)度均提高,而塑性不下降。王華等制備了含微量Sc、Zr的2524鋁合金板材,對(duì)其組織和性能研究表明微量 Sc 和 Zr 在 2524 鋁合金中主要以次生的 Al3(Sc,Zr)粒子形式存在,這種粒子與基體共格,釘扎位錯(cuò)和亞晶界,高溫固溶處理過程中仍然能夠抑制部分合金的再結(jié)晶。在 T3 狀態(tài)下,含 Sc、Zr 的 2524 鋁合金的塑性與 2524 鋁合金的相當(dāng),而屈服強(qiáng)度提高了18 MPa。微量Sc、Zr對(duì)Al-Cu-Mg 合金的強(qiáng)化作用主要來源于添加微量Sc、Zr 引起的細(xì)晶強(qiáng)化、亞結(jié)構(gòu)強(qiáng)化和析出強(qiáng)化。由于合金元素及其構(gòu)成第二相的影響,2000 系鋁合金板材在烘烤過程中容易出現(xiàn)軟化現(xiàn)象,且其抗應(yīng)力腐蝕能力差,嚴(yán)重限制了該系列板材在車身外板的應(yīng)用。
2
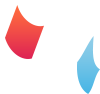
5000系合金的微合金化
5000 系合金是不可熱處理強(qiáng)化的鋁合金,具有中等的屈服強(qiáng)度和抗拉強(qiáng)度、耐蝕性、加工性能與良好的焊接性。Mg 溶于 Al 基體中形成固溶強(qiáng)化,使合金在屈服強(qiáng)度、抗拉強(qiáng)度、成形性和抗蝕性方面具有一般鋼材的特點(diǎn),所以日本廣泛應(yīng)用5000 系鋁合金作為汽車內(nèi)板材料(5022、5023、5182)以及其它形狀復(fù)雜的部件。5000 系合金的固溶強(qiáng)化存在延時(shí)屈服和勒德斯線 2 個(gè)明顯的缺點(diǎn),此外與6000系相比,5000系合金在噴漆退火后其屈服強(qiáng)度下降,而 6000 系的屈服強(qiáng)度上升。目前 5000 系鋁合金的研究通常是通過優(yōu)化合金成分、控制雜質(zhì)質(zhì)量分?jǐn)?shù)、添加微量元素改善合金性能。如在 5050、5150 基礎(chǔ)上添加微量 Mn(錳)、Ga(鎵)研究而成的5025,具有優(yōu)良的壓力加工性能、成形性能和耐腐蝕性[8]。近年來,在 Al-Mg 合金中同時(shí)添加Sc和Zr 元素的研究較多,采用Sc和Zr 復(fù)合微合金化可顯著提高合金的抗拉強(qiáng)度。
5000 系鋁合金中,隨 Mg 質(zhì)量分?jǐn)?shù)的增加,材料的伸長(zhǎng)率開始下降,但當(dāng)Mg質(zhì)量分?jǐn)?shù)超過2%以后,伸長(zhǎng)率會(huì)迅速上升,近年來還開發(fā)出了 Mg 的質(zhì)量分?jǐn)?shù)達(dá) 5%~6%的高鎂鋁合金板。另一方面,適當(dāng)?shù)丶尤?Mn 元素,使 Mg 相沉淀均勻,可以提高合金的抗腐蝕性能,同時(shí)能提高合金的再結(jié)晶溫度,抑制晶粒長(zhǎng)大,確保合金具有更高的穩(wěn)定性。研究發(fā)現(xiàn)向鋁中添加質(zhì)量分?jǐn)?shù)為1%的Mg,可以使材料的抗拉強(qiáng)度提高 35 MPa,而加入同量 Mn的效果則幾乎大了一倍。但 Mn 含量多時(shí),抗拉強(qiáng)度略有增加,塑性則顯著降低。尤其有微量 Na(鈉)存在時(shí),熱軋過程會(huì)產(chǎn)生“鈉脆”現(xiàn)象。
3
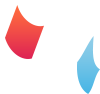
6000系合金的微合金化
奧林匹克運(yùn)動(dòng)會(huì)是國(guó)際奧林匹克委員會(huì)主辦的世界規(guī)模最大的綜合性運(yùn)動(dòng)會(huì),每四年一屆,會(huì)期不超過16日,是世界上影響力最大的體育盛會(huì)。
6000 系鋁合金是可熱處理強(qiáng)化的鋁合金,其成形性好、耐蝕性強(qiáng)、抗拉強(qiáng)度高、耐高溫性能較好。6000系鋁合金較7000系合金有較高的疲勞強(qiáng)度,又比 2000 系合金有較好抗腐蝕性能。5000 系合金的斯德勒線及桔皮效應(yīng)不令人滿意,6000 系合金上述 2 種性質(zhì)較好。6000 系合金可以通過添加少量多種合金元素來細(xì)化晶粒,改變?cè)俳Y(jié)晶狀態(tài),同時(shí)改進(jìn)鑄造、軋制及熱處理工藝獲得良好的綜合性能。6000 系鋁合金的時(shí)效過程就是過飽和固溶體的脫溶分解過程,也是原子擴(kuò)散過程,與時(shí)效時(shí)間和溫度都有關(guān)。自然時(shí)效使人工時(shí)效后合金的抗拉強(qiáng)度、硬度下降,而預(yù)時(shí)效則能減輕自然時(shí)效的有害作用。在固溶處理之后引入預(yù)應(yīng)變會(huì)大大抑制 GP(溶質(zhì)原子富集區(qū))的形成,加速中間相的形核和長(zhǎng)大。預(yù)應(yīng)變可充分發(fā)揮6000系鋁合金車身板的烘烤硬化效應(yīng)。
6000系合金中除Al 以外,最多的元素是Mg 和Si(硅)。Mg 能提高合金的抗蝕性和可焊性。增加Mg 的質(zhì)量分?jǐn)?shù)有利于提高合金的抗拉強(qiáng)度,但不利于合金的沖壓成形。隨含 Mg 的質(zhì)量分?jǐn)?shù)的增加,合金的抗拉強(qiáng)度升高,但其作用有一定的范圍,當(dāng)其質(zhì)量分?jǐn)?shù)達(dá)到 1.7%時(shí),合金的抗拉強(qiáng)度明顯降低 。6000系合金中的強(qiáng)化相是Mg2Si。研究表明,合金中強(qiáng)化相 Mg2Si 的質(zhì)量分?jǐn)?shù)每增加 0.1%,抗拉強(qiáng)度峰值可增加 5 MPa 左右,同時(shí)延伸率也有少量增加,如表 1 所示。除形成強(qiáng)化相以外,Si 能提高鑄造和焊接流動(dòng)性、耐磨性。相對(duì)強(qiáng)化相 Mg2Si 來說,Si 的質(zhì)量分?jǐn)?shù)通常是過量的。研究表明,Si 質(zhì)量分?jǐn)?shù)過量時(shí)析出次序以及各亞穩(wěn)相的結(jié)構(gòu)及其晶格常數(shù)不會(huì)改變,但析出相的化學(xué)成分及密度發(fā)生變化。過量的 Si 更易析出大量的團(tuán)簇,更易形成細(xì)小均勻分布的β’’相,使合金密度大大增加,提高合金的抗拉強(qiáng)度。
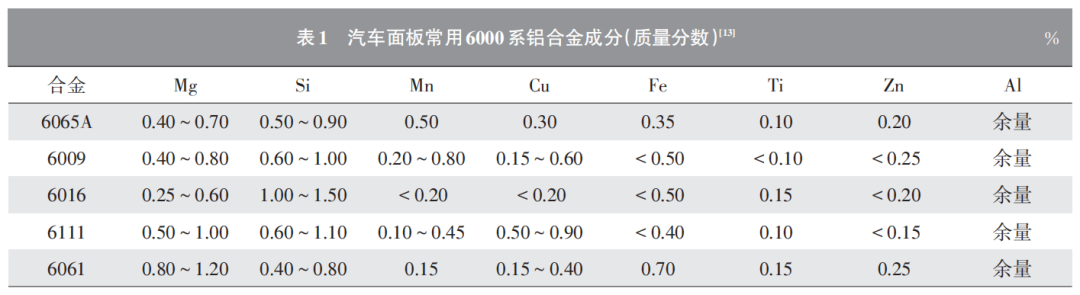
隨著 Cu 質(zhì)量分?jǐn)?shù)增加,T4 態(tài)合金板材的抗拉強(qiáng)度單調(diào)增大,n值(加工硬化指數(shù))呈現(xiàn)出略有增大的趨勢(shì),延伸率、r值(各向異性指數(shù))變化規(guī)律不明顯,IE 值單調(diào)下降,板材的拉脹成形性能變差;隨著 Cu 質(zhì)量分?jǐn)?shù)增加,T4 態(tài)合金板材烤漆前后的抗拉強(qiáng)度均單調(diào)增大,但合金板材模擬烤漆后表現(xiàn)出烤漆軟化現(xiàn)象,且其軟化量隨 Cu 質(zhì)量分?jǐn)?shù)增加而逐漸增大,說明 Cu 質(zhì)量分?jǐn)?shù)增加不利于鋁板烘烤硬化性能的發(fā)揮。170 ℃×30 min 的模擬 烤漆處理過程由于溫度較低,且時(shí)間很短不足以 使T4態(tài)合金薄板基體中析出具有明顯強(qiáng)化作用的過渡相,同時(shí)Cu質(zhì)量分?jǐn)?shù)增加還促進(jìn)T4態(tài)合金薄 板中已經(jīng)存在的GP區(qū)大量回溶,是T4態(tài)合金薄板 經(jīng)模擬烤漆處理后其抗拉強(qiáng)度降低量隨Cu質(zhì)量分?jǐn)?shù)增加而逐漸增大的根本原因。6000 系合金中添加微量的 Mn 元素時(shí),Mn 彌散相質(zhì)點(diǎn)的亞結(jié)構(gòu)強(qiáng)化和Mn的彌散析出強(qiáng)化以及β’’相的時(shí)效強(qiáng)化作用可使合金的抗拉強(qiáng)度顯著提高。
6063 鋁合金通過添加 Ti(鈦)、B(硼)和 Re (錸)進(jìn)行晶粒細(xì)化,結(jié)果表明,同時(shí)加入Ti、B和Re的6063 合金的組織比只加Ti或者Ti和Re的合金組織細(xì)小。通過 Ti、Ti+Re 或 Ti+Re+B 細(xì)化的 6063 合金均有較好的時(shí)效行為。經(jīng)較短的時(shí)效時(shí) 間硬度就可達(dá)到峰值硬度,在 200 ℃時(shí)效 6 h 時(shí)其 硬度無明顯降低。Re 加入形成 Al-Si-Mg-Re 中間 金屬化合物導(dǎo)致合金的抗拉強(qiáng)度比加Ti的低。
4
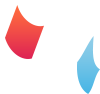
鋁合金的熱處理
奧林匹克運(yùn)動(dòng)會(huì)是國(guó)際奧林匹克委員會(huì)主辦的世界規(guī)模最大的綜合性運(yùn)動(dòng)會(huì),每四年一屆,會(huì)期不超過16日,是世界上影響力最大的體育盛會(huì)。
熱處理對(duì)合金的組織和性能有很大的影響。鋁合金的熱處理主要包括退火處理、固溶處理、時(shí)效處理、回歸再時(shí)效處理以及最終形變熱處理。5000 系合金是不可熱處理強(qiáng)化合金,因而其熱處理工藝主要是退火處理。5000 系鋁合金板經(jīng)退火處理后,其抗拉強(qiáng)度略有下降,而延伸率和應(yīng)變硬化指數(shù)大幅地提高。退火溫度升高,使板材抗拉強(qiáng)度降低,延伸率增大。文獻(xiàn)[18]得出5754-H24鋁合金板材的退火溫度范圍為240~250 ℃,保溫時(shí)間 1 h。5083 鋁合金板在 300 ℃退火后抗拉強(qiáng)度大幅度降低,塑性明顯提高。在 550 ℃退火時(shí),軋制態(tài) 5083 鋁合金板材的纖維組織消失,再結(jié)晶晶粒明顯長(zhǎng)大,并等軸化。
2000 系和 6000 系合金是可熱處理強(qiáng)化合金,因而常用固溶處理、時(shí)效處理、回歸再時(shí)效處理以及最終形變熱處理方式改善其組織和性能。固溶處理后通常進(jìn)行時(shí)效處理,固溶處理使強(qiáng)化相最大限度溶入基體,而時(shí)效處理則使強(qiáng)化相從基體中析出,從而使合金的硬度增加。鋁合金經(jīng)固溶+時(shí)效處理后,再次加熱到比時(shí)效更高的溫度,保溫一段時(shí)間后,快速冷卻使材料恢復(fù)到固溶處理狀態(tài),此時(shí)對(duì)材料再次進(jìn)行時(shí)效處理可以使其屈服及抗拉強(qiáng)度繼續(xù)升高,這一熱處理過程即回歸再時(shí)效熱處理。最終形變熱處理是在鋁合金經(jīng)固溶+時(shí)效處理后,進(jìn)行一定量的冷變形,然后再進(jìn)行最終時(shí)效熱處理,通過這種熱處理工藝,鋁合金材料的屈服強(qiáng)度可以得到很大程度提高。
熱處理后鋁合金板材的最終性能受溫度、時(shí)間因素的影響。鋁合金退火時(shí),板材的抗拉強(qiáng)度隨退火溫度的升高而降低。淬火時(shí)板材的抗拉強(qiáng)度、伸長(zhǎng)率隨淬火加熱溫度的升高而增加。進(jìn)行時(shí)效熱處理時(shí),隨著時(shí)效熱處理保溫時(shí)間延長(zhǎng),板材的抗拉強(qiáng)度升高,電導(dǎo)率逐漸增加,但保溫到一定時(shí)間時(shí)出現(xiàn)峰值后開始下降。熱處理工藝對(duì)鋁合金板材的力學(xué)性能和應(yīng)力腐蝕敏感性有影響,2519鋁合金板材經(jīng)先高溫后低溫的雙級(jí)時(shí)效處理(180 ℃×3 h+145 ℃×24 h)后力學(xué)性能最好,但抗應(yīng)力腐蝕性能最差;經(jīng)形變熱處理(20 ℃×100 h+預(yù)變形15%+145 ℃×21 h)后的力學(xué)性能較好,抗應(yīng)力腐蝕性能最好;過時(shí)效狀態(tài)(180 ℃×30 h)下力學(xué)性能最差,抗應(yīng)力腐蝕性能適中。2000 系鋁合金的屈服強(qiáng)度比較高,熱處理進(jìn)行自然時(shí)效時(shí)其屈服強(qiáng)度進(jìn)一步增加,之后的成形難度增加。在自然時(shí)效前,對(duì)其進(jìn)行短時(shí)間的預(yù)時(shí)效,能夠抑制隨后時(shí)效過程中 GP 區(qū)的形成,降低自然時(shí)效的硬化效果,同時(shí)提高合金的應(yīng)變硬化指數(shù)和延伸率,從而提高合金板材的成形性,如圖1所示。6022鋁合金在 500~560 ℃進(jìn)行固溶處理時(shí),晶粒大小基本不變,而第二相數(shù)量顯著減少,超出該溫度范圍后晶粒粗化。560 ℃固溶處理后自然時(shí)效可獲得最佳力學(xué)性能。時(shí)效前進(jìn)行預(yù)時(shí)效,能有效抑制自然時(shí)效的不良影響并提高模擬烤漆后的烤漆性能。
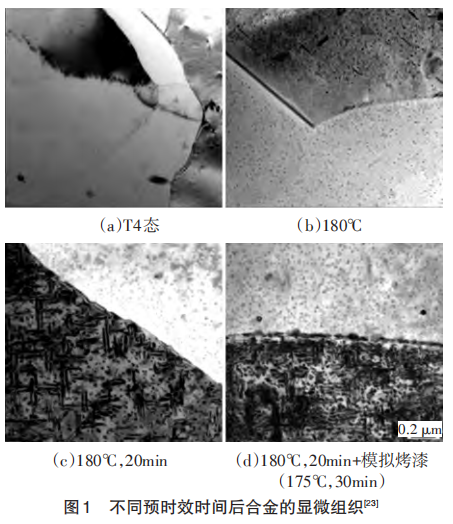
三、車身用鋁合金板的先進(jìn)成形技術(shù)
與鋼相比,用于車身板的鋁合金通過合金成分的調(diào)整以及熱處理工藝的制定可以達(dá)到相應(yīng)的力學(xué)性能,但其成形性方面仍然存在不小的差距。對(duì)于具有一定沖壓深度和形狀要求的覆蓋件,采用鋁合金進(jìn)行室溫沖壓時(shí)容易產(chǎn)生裂紋、起皺,并發(fā)生回彈,影響零件的表面質(zhì)量和尺寸精度。因而,鋁合金要代替鋼鐵材料而廣泛應(yīng)用于汽車覆蓋件,就必須改善并研發(fā)新的鋁合金成形工藝。鋁合金先進(jìn)成形技術(shù)主要包括液壓成形、溫成形、控制壓邊力成形以及超塑性成形。
1
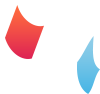
液壓成型
板材液壓成形是在模腔內(nèi)充滿液體的狀態(tài)下將材料置于模面上,材料隨沖頭的前進(jìn)被壓人充滿液體的模腔內(nèi),同時(shí)被液體產(chǎn)生的壓力緊貼沖頭,從而形成“摩擦保持效果”;而且液體可以從板料法蘭與凹模間溢出,減少有害摩擦阻力而形成“溢流潤(rùn)滑效果”,因此使板料的成形極限得到極大的提高。板材液壓成形利用靜水壓提高深拉延比并減少成形工件的厚度。常規(guī)沖壓只有 2.0 左右極限深沖比的鋁合金板,用該成形方法沖壓可將極限沖壓比提高到 2.3,超過軟鋼常法沖壓的極限深沖比。有研究者使用一種輔以浮動(dòng)圓盤的液壓成形模具對(duì) 6061 板材進(jìn)行成形。經(jīng)試驗(yàn)發(fā)現(xiàn),使用這種新的液壓成形模具對(duì)板材進(jìn)行成形時(shí),液壓成形過程的壓邊力、模腔壓力與成形力均減小。郎利輝對(duì)鋁合金 2B06 覆層板在三向應(yīng)力作用下的成形性能進(jìn)行了研究,板材發(fā)生頸縮時(shí)整體應(yīng)變比單層板更大,成形板的等效應(yīng)力減小,流動(dòng)特性得到改善。
2
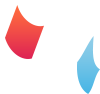
溫成形
隨著溫度升高,材料的成形性增加。通常,在材料的再結(jié)晶溫度以上的成形過程稱為熱成型,而材料在回復(fù)或再結(jié)晶溫度以下、常溫以上進(jìn)行的成形工藝稱為溫成形。ZHONG H等在不同的溫度條件下試驗(yàn)所獲得的成形極限圖表明,隨著溫度升高,成形極限曲線升高,板料的成形性提高。但用不同成形速度進(jìn)行試驗(yàn),成形速度過快時(shí),即使是在較高的溫度條件下,材料的成形性也無顯著提高。LI等對(duì)5000系和6000系鋁合金板材在不同溫度條件下進(jìn)行深拉試驗(yàn),得到了較優(yōu)的成形溫度及其它的成形工藝條件。從合金熱處理特性來看,5000 系鋁合金板在溫成形溫度區(qū)間內(nèi)成形性顯著提高,易于控制,已有 5182-O 門內(nèi)板、5083發(fā)動(dòng)機(jī)罩等產(chǎn)品試制案例;而6000系鋁合金板由于組織受溫度影響較大,成形條件苛刻,產(chǎn)品的組織和性能難以控制。
3
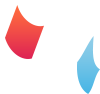
控制壓邊力成形
壓邊力是板料成形技術(shù)中的重要控制手段,在實(shí)際深拉的過程中理想的壓邊力應(yīng)該是變化的。韓丹瑩等通過采用多級(jí)壓邊力方法,在成形初期和中期允許法蘭輕微起皺的前提下使用低的防皺壓力,在成形后期使用高的壓邊力從而消除這種輕微的起皺,達(dá)到提高工件成形極限的目的。傳統(tǒng)的壓邊方式是采用剛性壓邊圈,壓邊力均勻分布在壓邊圈上。對(duì)于表面形狀復(fù)雜的深拉件,深拉成形過程中金屬材料的流動(dòng)在各個(gè)部分是不均勻的,如果都采用恒定的均勻壓邊力,可能導(dǎo)致在同一零件上同時(shí)出現(xiàn)起皺和拉裂的現(xiàn)象。彈性結(jié)構(gòu)的壓邊裝置可以比較好地解決這個(gè)問題。余海燕等對(duì)鋁合金板進(jìn)行研究,以階梯盒形件為研究對(duì)象進(jìn)行深沖試驗(yàn),通過多點(diǎn)壓邊力控制系統(tǒng)對(duì)恒壓邊力和變壓邊力方案的效果進(jìn)行比較,結(jié)果發(fā)現(xiàn),變壓邊力方案下的工件基本消除了恒壓邊力方案中出現(xiàn)的起皺和破裂,得到了很好的效果。
MUSTAFA 等采用不同的壓邊力對(duì)盒型件進(jìn)行不同深度的拉深試驗(yàn),研究壓邊力對(duì)其成形的影響。結(jié)果表明,壓邊力是時(shí)間的函數(shù),通過控制壓邊力的變化,可以提高材料的成形性以及最終獲得高質(zhì)量零件。同時(shí)壓邊力還應(yīng)與位置有關(guān)。通過對(duì)壓邊力的一系列控制,起皺現(xiàn)象得到很好的緩解,但并未完全消除。
4
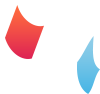
超塑性成形
奧林匹克運(yùn)動(dòng)會(huì)是國(guó)際奧林匹克委員會(huì)主辦的世界規(guī)模最大的綜合性運(yùn)動(dòng)會(huì),每四年一屆,會(huì)期不超過16日,是世界上影響力最大的體育盛會(huì)。
超塑性成形是指板材在一定的變形溫度和變形速度條件下產(chǎn)生超塑性后的成形,鋁合金的超塑性溫度范圍為 500~550 ℃,比溫成形的溫度高許多。超塑性成形能加工常規(guī)沖壓工藝不能成形的復(fù)雜零件。超塑性成形法可分為陽模成形法和陰模成形法。陽模成形法適用于大型的淺成形件,而陰模法則適用于深成形件和復(fù)雜的成形件。
TROEGER等對(duì)6000系合金的超塑性研究表明,500 ℃以上時(shí)合金表現(xiàn)出超塑性。在 540 ℃應(yīng)變速率為2×10-4~5×10-4 /s時(shí),應(yīng)變速率敏感性達(dá)到最大值0.5 /s。應(yīng)變速率為5×10-4 /s時(shí)合金的單向拉伸延伸率最大達(dá)375%,對(duì)應(yīng)的流變應(yīng)力為4.7 MPa,如圖2所示。周義等用鋁合金以超塑性成形方式進(jìn)行了汽車前擋泥板成形試驗(yàn),在成形溫度控制在450~500 ℃、最大脹形壓力達(dá)到0.42 MPa的條件下,試驗(yàn)取得成功,整個(gè)成形時(shí)間為 30~60 min。梁繼業(yè)等以 5083 鋁合金為研究對(duì)象對(duì)車門的鋁合金外板的正反脹超塑性成形工藝進(jìn)行了研究,在480 ℃和應(yīng)變速率為 1×10-3 /s 條件下,最大伸長(zhǎng)可達(dá)到242%。雖然超塑性成形時(shí)間比一般成形工藝時(shí)間長(zhǎng),但在成形時(shí)材料塑性流動(dòng)的阻力非常小,即使是復(fù)雜件也可以一次成形,因而其應(yīng)用前景非常廣泛。
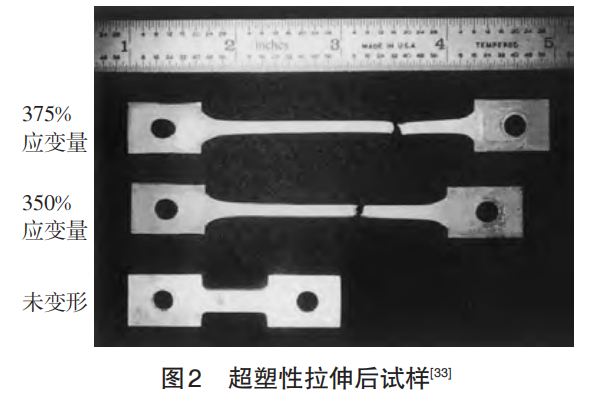
車身用鋁合金成形的有限元模擬
鋁合金板材成形過程中,存在的問題主要有起皺、破裂和回彈。隨著有限元模擬的發(fā)展,越來越多的研究者使用有限元法模擬板材的成形過程。若要準(zhǔn)確模擬實(shí)際工藝過程,必須建立準(zhǔn)確的材料模型和屈服準(zhǔn)則以及設(shè)置適當(dāng)?shù)墓に噮?shù),如摩擦因數(shù)、壓邊力和成形速度。有限元模擬除了對(duì)成形進(jìn)行預(yù)測(cè)外,常用于優(yōu)化成形工藝、設(shè)計(jì)工藝補(bǔ)充面以及設(shè)計(jì)坯料尺寸。通過分析不同工藝條件下工件的成形性,獲得能最大程度發(fā)揮材料成形性的工藝參數(shù)。
1
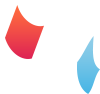
材料模型與屈服準(zhǔn)則
材料的模型主要包括材料的應(yīng)力-應(yīng)變曲線、彈性模量、硬化指數(shù)、塑性應(yīng)變比、泊松比。其中,材料的流變應(yīng)力方程是材料模型里面最主要的部分之一。為準(zhǔn)確模擬實(shí)際變形過程,必須有能夠準(zhǔn)確描述材料屈服行為的屈服準(zhǔn)則。目前用于描述塑性變形的屈服準(zhǔn)則主要有 Von-Mises 屈服準(zhǔn)則、Tresca屈服準(zhǔn)則以及Hill屈服準(zhǔn)則。SIGUANG XU 等對(duì) Hill 屈服準(zhǔn)則進(jìn)行研究,通過6111鋁合金試驗(yàn)數(shù)據(jù)比較基于 Hill’s 1948 和Hill’s 1993屈服準(zhǔn)則對(duì)與極限應(yīng)變的預(yù)測(cè),結(jié)果表明 Hill’s 1993 屈服準(zhǔn)則可以很好描述鋁合金板材局部縮頸行為。陳忠家等基于合金材料塑性變形過程中位錯(cuò)和溶質(zhì)原子間相互作用的分析,建立了一個(gè)可用于描述鋸齒形屈服現(xiàn)象的唯象本構(gòu)模型。該模型將溶質(zhì)原子對(duì)位錯(cuò)運(yùn)動(dòng)的釘扎效應(yīng)和位錯(cuò)掙脫后的脫釘效應(yīng)置于一個(gè)統(tǒng)一的框架內(nèi)進(jìn)行考慮,而這2個(gè)效應(yīng)的相互競(jìng)爭(zhēng)將決定材料宏觀變形行為的發(fā)展演化。基于該模型的數(shù)值模擬結(jié)果和試驗(yàn)測(cè)試結(jié)果取得了良好的一致性,從而驗(yàn)證了理論和模型的有效性。
通常在對(duì)不銹鋼板各向異性材料進(jìn)行模擬時(shí)多使用 Von-Mises 或 Hill-48 屈服準(zhǔn)則圈間的摩擦系數(shù)變化對(duì)沖壓結(jié)果的影響比坯料與凹模間摩擦系數(shù)變化所產(chǎn)生的影響大,坯料與凹模之間的摩擦系數(shù)越大,對(duì)沖壓結(jié)果就越不利,但這種不利影響隨著坯料與凹模之間摩擦系數(shù)的進(jìn)一步增大而明顯減弱。在沖壓條件不太理想時(shí),僅僅依靠壓邊力的調(diào)整難以獲得理想結(jié)果,不論沖壓條件如何,壓邊力都存在一個(gè)最優(yōu)值。
板材沖壓成形過程中受許多工藝參數(shù)的影響,通過有限元模擬可以分析各參數(shù)對(duì)其影響規(guī)律,但不能通過簡(jiǎn)單的參數(shù)組合獲得最佳的成形工藝。通過正交設(shè)計(jì)模擬分析各參數(shù)對(duì)板材成形性的影響,不但可以大大節(jié)約計(jì)算時(shí)間,而且可以獲得最佳的成形工藝。汽車覆蓋件成形時(shí),沖壓速度對(duì)產(chǎn)品質(zhì)量的影響作用大于壓邊力、拉延筋和摩擦系數(shù)對(duì)產(chǎn)品質(zhì)量的影響,沖壓速度越大,產(chǎn)品的局部厚度越小。在模擬過程中發(fā)現(xiàn),通過拉延筋的分布以及拉延阻力的設(shè)置,可以消除零件起皺和開裂現(xiàn)象。對(duì)成形后回彈量分析發(fā)現(xiàn),成形質(zhì)量好的工藝,其回彈量也小。
除成形工藝參數(shù)外,坯料的初始形狀和網(wǎng)格的自適應(yīng)技術(shù)、單元屬性對(duì)沖壓結(jié)果也會(huì)產(chǎn)生影響。研究發(fā)現(xiàn),進(jìn)行模擬成形時(shí),若能促進(jìn)板料的初始形狀更好地與材料的流動(dòng)規(guī)律相適應(yīng),就能改善板料最終的成形質(zhì)量。通過對(duì)坯料局部形狀的調(diào)整能進(jìn)一步消除成形缺陷。在模擬時(shí)采用自適應(yīng)網(wǎng)格技術(shù)能夠在保證成形模擬精度的同時(shí)避免計(jì)算效率的下降。板料成形時(shí),由于其厚度很小,因而通常采用2號(hào)BT殼單元,采用該單元進(jìn)行模擬有較高的精度和較高的效率。成形時(shí)常在厚度方向上采用 3 個(gè)積分點(diǎn),若進(jìn)行回彈分析,則需采用16號(hào)全積分單元,并選用7個(gè)積分點(diǎn)。
覆蓋件成形時(shí)發(fā)生彈性和塑性變形,卸載后彈性變形部分恢復(fù)而發(fā)生回彈現(xiàn)象。覆蓋件的回彈嚴(yán)重影響產(chǎn)品的尺寸精度和表面質(zhì)量,因而需要對(duì)產(chǎn)品回彈進(jìn)行預(yù)測(cè)并加以控制。目前主要用有限元法對(duì)成形后的回彈進(jìn)行研究。張凇等使用 Dynaform 有限元軟件對(duì)汽車底座橫梁外板的沖壓成形后回彈進(jìn)行仿真研究,并將回彈的模擬結(jié)果與試驗(yàn)結(jié)果進(jìn)行比較,發(fā)現(xiàn)二者十分吻合,模擬能夠準(zhǔn)確預(yù)測(cè)成形后的回彈。
文獻(xiàn)研究了板料成形過程中材料參數(shù)和工藝參數(shù)等對(duì)回彈的影響規(guī)律。回彈量的大小與材料的屈服強(qiáng)度、厚向異性系數(shù)成正比,與材料的彈性模量和硬化指數(shù)成反比。減小模具間間隙可以減小板料成形后的回彈量。隨著壓邊力減小和凸模的圓角半徑增大,回彈角增大。隨著摩擦系數(shù)增大,回彈量減小。板料的厚度對(duì)成形后產(chǎn)品的回彈也有一定影響,板料厚度增加,成形后其回彈量減小。通過對(duì)各因素的正交分析發(fā)現(xiàn),在相同的成形條件下,材料參數(shù)對(duì)回彈的影響最大,摩擦系數(shù)次之,壓邊力再次之,板料的厚度影響最小。
除研究各因素對(duì)回彈的影響外,張引引等考慮鋁合金板材與模具間的接觸演變過程,建立了一個(gè)有限元模型來預(yù)測(cè)鋁合金板材變形后的回彈。模型中板材本構(gòu)方程采用基于更新拉格朗日彈塑性的材料模型,卸載過程采用模具反向運(yùn)動(dòng)方法。對(duì)有限元敏感度分析發(fā)現(xiàn),回彈大小和整體精度受到元素大小、積分點(diǎn)和屈服準(zhǔn)則的影響很大。將模擬結(jié)果與試驗(yàn)對(duì)比分析,發(fā)現(xiàn)二者較好吻合。通過有限元分析得到了一個(gè)優(yōu)化的模型,提供了一個(gè)更加精確的方法。
結(jié)束語
鋁合金板材用于汽車車身,既有明顯的輕量化和節(jié)能效果,又符合安全環(huán)保及汽車用材的發(fā)展趨勢(shì)。近年來,研究者對(duì)鋁合金汽車板生產(chǎn)的關(guān)鍵環(huán)節(jié)進(jìn)行了大量研究,為推動(dòng)鋁合金板材在汽車車身上的廣泛應(yīng)用打下了堅(jiān)實(shí)基礎(chǔ)。鋁合金微合金化方面,著重研究 5000 系和 6000 系典型牌號(hào)材料中控制合金成分及含量對(duì)材料性能的影響規(guī)律,并探索鋁板性能與熱處理工藝的耦合關(guān)系;熱處理方面以6000系的固溶和時(shí)效組合工藝為研究重點(diǎn)。此外,在應(yīng)用端為解決鋁合金板材沖壓成形缺陷,一方面通過開發(fā)新的工藝以適應(yīng)材料的性能和零部件的功能,另一方面采用試驗(yàn)和仿真相結(jié)合的方式研究回彈、開裂的成因,在高精度材料模型的基礎(chǔ)上,提出缺陷改善及控制措施??傮w而言,鋁合金板材已廣泛應(yīng)用于覆蓋件,在鋁合金板材生產(chǎn)方面也實(shí)現(xiàn)了國(guó)產(chǎn)化。在未來的發(fā)展中,研究的重點(diǎn)仍將圍繞材料的成分設(shè)計(jì)和生產(chǎn)工藝的匹配方面,以實(shí)現(xiàn)性能穩(wěn)定、優(yōu)良的板材的穩(wěn)定化生產(chǎn)。
來源:汽車輕量化技術(shù)創(chuàng)新戰(zhàn)略聯(lián)盟